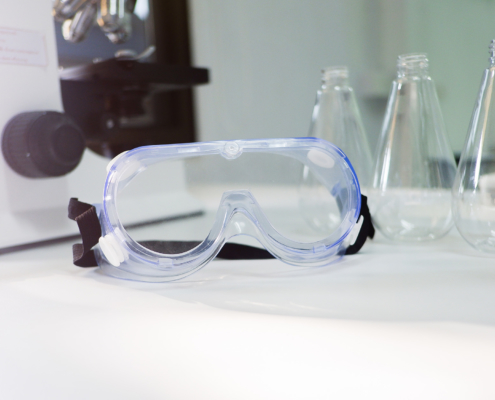
How to Plan an Inventory of Your Chemical Safety Equipment
Every business prepared to handle chemicals in their day-to-day operations must make sure its safety products are up to date and ready to be used. That’s why it’s important to annually check your inventory of chemical safety products, such as chemical measuring containers, protective gloves, and more to ensure they are readily available. Whether you’re a small business or a large operation, getting your chemicals in order is essential for ensuring that your employees remain safe when handling them.
How to Assess Your Existing Chemical Safety Equipment
First, review your existing inventory to analyze equipment use patterns, as well as consider any new products needed for the upcoming year. For example, if your business has recently added a new chemical process or increased production levels, then you’ll need to make sure that you have enough supplies to meet the demands, including:
- Chemical Measuring Jug
- Chemical Handling Gloves
- Face Masks
- Goggles
- Aprons
- Containment Basins
- Ventilation Systems
- Respirators
- Portable Gas Detectors
- pH Meters
- Spill Kits
- Storage Cabinets & Containers
If any existing equipment is damaged, shows general wear-and-tear, or could lead to exposure, replace it. Furthermore, document and double-check the expiration dates on any chemicals already in stock. This will prevent outdated materials from being used and give your business ample time to restock.
Develop an Ongoing Inventory Plan
The next step is to create a comprehensive timeline that documents each step to be completed and schedules regular inventory checks for at least once a year. Businesses that work with particularly hazardous materials or highly volatile chemicals need more frequent reviews (e.g., quarterly or monthly).
Make sure that all employees involved are aware of this timeline so they can plan accordingly. Developing a recurring plan around chemical safety equipment ensures that they can always access the proper equipment when and where they need it, protecting them, your business, and your customers.
Factoring in Hazardous Materials Review
It’s also essential to stay up-to-date on all applicable laws and regulations governing hazardous materials. This includes knowing any new labeling requirements (e.g. storage containers must include relevant hazard symbols), as well as understanding which chemicals require specific safety measures (e.g., wearing protective gloves).
Businesses must train employees on a system for safe handling and disposal. Furthermore, they should keep records of all hazardous materials used and regularly check for any issues such as leaks or spills. By staying compliant with regulations, they can protect their employees from potential harm or legal action.
Does your business sell or handle chemicals? If so, you need to ensure your employees are using them safely. Our line of chemical safety products can help. From prepackaged items to custom options, Axiom Products has what you need.
Reviewing Storage Containers and Labels
In order to ensure proper storage of chemicals and prevent any accidents, businesses should routinely check all associated containers at least once a year, if not more. Make sure that all labels clearly identify the contents as well as convey any relevant warning information regarding safe use and handling (if applicable). Any containers that hold expired chemicals, or at least ones that haven’t been used in over 12 months, should be safely disposed of before they become workplace hazards.
How to Tell When Chemical Safety Equipment Needs to Be Replaced
As part of your inventory, be sure to inspect all pieces of chemical safety equipment, such as goggles and aprons. Look for any cracks, tears, discoloration, or fading that may have occurred due to age, regular use, or chemical exposure.
Depending on the type of chemical that was used, some items may need to be disposed of immediately after use in order to prevent any potential health risks from occurring. For example, chemical measuring jugs should be discarded after being used with highly corrosive substances such as hydrochloric acid or sodium hydroxide solutions. Chemical handling gloves are very prone to decay, and should be replaced if they have come into contact with similarly hazardous materials.
Do You Need to Replace Your Chemical Safety Equipment?
Having an annual inventory check of your chemical safety products is essential for ensuring compliance with applicable laws and regulations governing their use, as well as preventing potential accidents from occurring in the workplace environment due to worn-out equipment. If you need help replacing any of your chemical safety equipment, contact Axiom today!